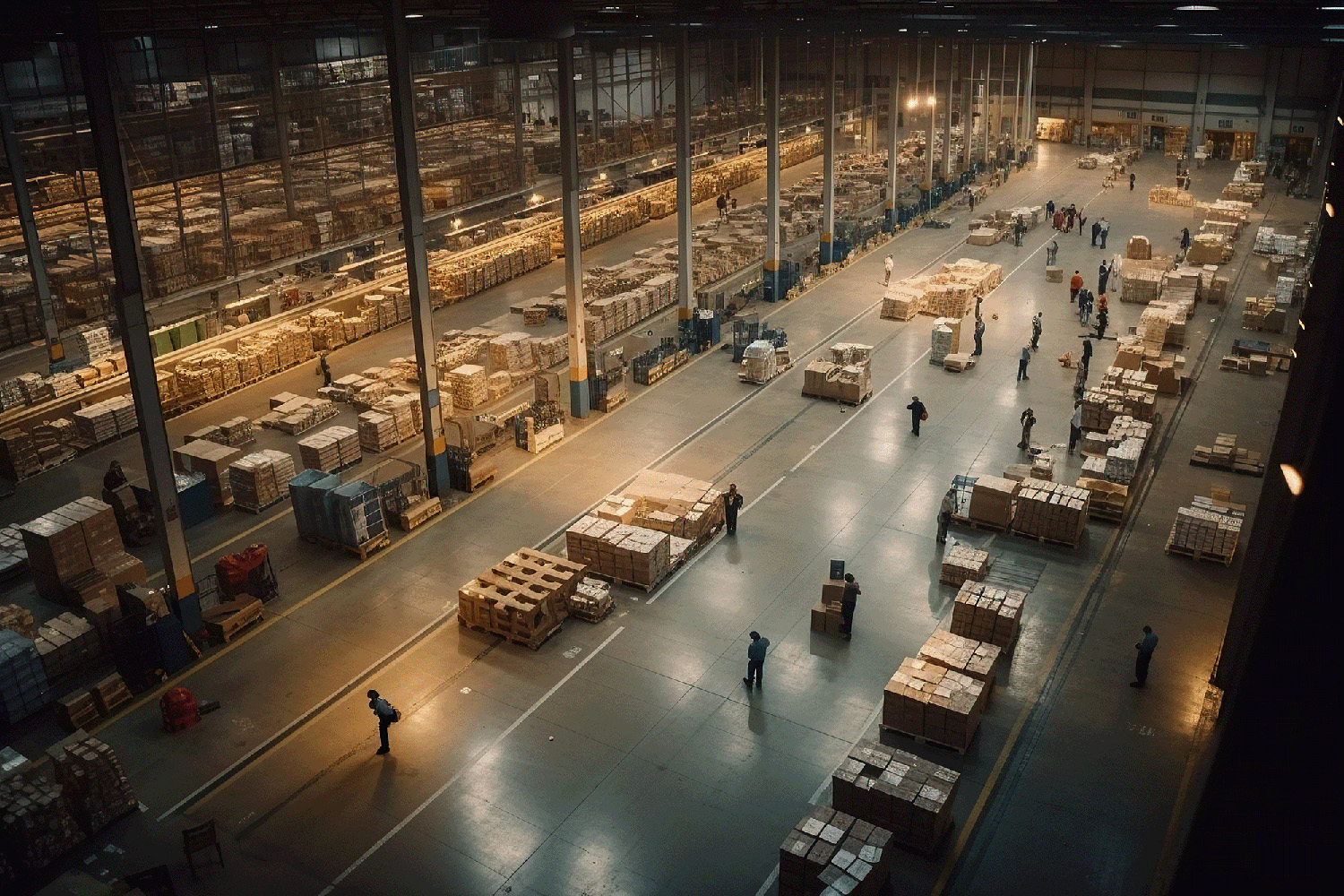
31 Jan How to Implement a QMS? Quality Management System
Are you considering a QMS for your business? Navigating the complex world of business management can be challenging, especially when trying to align your objectives with financial goals. One strategy that may help streamline operations and boost productivity is the implementation of a Quality Management System (QMS).
So, how to implement a QMS?
In this blog post, we’ll explore the concept of QMS, its benefits, and how to implement a QMS system in your business.
What is a QMS?
A QMS system helps businesses plan and execute their core functions more efficiently. It provides a framework of policies, procedures, and processes. A QMS focuses on improving efficiency and effectiveness while adhering to any regulatory or statutory obligations an organization might have.
The primary aim of a QMS is to ensure quality control over products and services, ultimately driving customer satisfaction. It also facilitates continuous improvement, an essential element in today’s fast-paced business environment.
A QMS can be customized to fit any organization. It can be customized regardless of its size or sector. It is not a one-size-fits-all solution. Adopting a QMS encourages a culture of quality that extends beyond compliance, encompassing every aspect of the business, and driving operational excellence.
A successful QMS should integrate seamlessly with existing business operations, aligning with the company’s strategic objectives. This integration allows for better decision-making, communication, and transparency across all departments.
The QMS is not just about identifying and solving problems. Adopting a proactive approach to quality, identifying opportunities for improvement, and making continuous enhancements is what it’s about. This strategy enables businesses to remain competitive, meet customer expectations, and achieve their financial objectives.
A QMS is important for organizations to improve productivity, satisfy customers, and continuously improve their processes. It’s a strategic approach to managing quality and a crucial component in the successful running of any business.
Should You Implement a QMS?
Before starting a QMS, it’s important to consider its importance and how it can benefit your business. Implementation is a strategic move that requires a substantial commitment to ongoing improvement and customer satisfaction.
A well-used QMS can improve business, make customers happier, and create a strong base for sustainable growth. Further, it can also aid in identifying and addressing operational inefficiencies, potentially resulting in considerable cost savings.
However, it’s essential to remember that the decision to implement QMS software should be based on a comprehensive understanding of your business’s unique attributes, resource availability, and long-term goals.
Don’t rush the decision. Assess if your business needs a QMS carefully before making a choice. Analyze your current quality control measures, customer feedback, and business processes before deciding.
Upon positive evaluation, a QMS can provide a structured and standardized approach to achieving higher quality standards and consistently meeting customer expectations. But it’s crucial to remember that a QMS is not a magic solution to all business problems. It demands consistent efforts, resource allocation, and the willingness to embrace change for improved outcomes.
A QMS helps with quality, but its success relies on the organization’s culture and employees’ commitment to quality. If your team is willing to embrace this change and dedicated to continuous improvement, a QMS can significantly transform your business operations, increasing efficiency and profitability.
Choosing a QMS That Fits Your Business
The decision to implement a QMS is a strategic one that should reflect the nuances of your business. In making this selection, you must take into account several critical factors. Your company’s size, protocols, and resources determine the best QMS for you.
A QMS should offer user-friendliness and flexibility, adapting smoothly to your business requirements. Your QMS should support your company’s growth regardless of size and not hinder your daily work.
Industry-specific QMSs can provide a tailored approach, finely tuned to the unique demands of your sector. However, there are also more generalized options that could offer broader applicability. The main thing is ensuring the QMS matches your industry and helps you achieve your business goals.
While browsing options, it’s wise to look for a QMS that aligns with recognized industry standards. This alignment often signifies that the QMS has been through rigorous testing and has proven effective in various scenarios. Plus, having a standard-compliant QMS might improve your company’s image in the eyes of stakeholders and customers.
The selection process is an integral part of your QMS journey. You have the opportunity to explore the details of your business. Focus on areas that would benefit from a structured, quality-oriented approach.
The goal is not only to have a QMS. The goal is also to create a quality-focused culture. This culture will drive your business to improve and excel in operations constantly.
Take your time and choose wisely, considering the long-term impact of your decision.
Developing a QMS Implementation Plan
The steps to implementing a QMS begins with the establishment of your quality goals. These goals, articulated in a quality policy, guide your commitment to quality assurance and customer satisfaction. After defining your goals, it’s time to recognize the procedures and processes that will aid in accomplishing these objectives.
Creating detailed documentation of these processes is an essential step, as this forms the blueprint for your QMS. Not only should these processes be documented, but they should also be effectively communicated and understood across the organization. Ensuring everyone is on the same page helps promote a culture of quality and fosters alignment with the company’s strategic goals.
Next in line is one of the most critical aspects of implementing a QMS – training your employees.
Your team needs to know the basics of quality management and the specific procedures of your QMS. Additionally, they should clearly understand their roles within the system. Training gives employees the knowledge and skills to work in the QMS and shows the organization values quality management.
Continuous assessment and improvement become key once the QMS is in place and operational. Regular audits offer a systematic way to assess the effectiveness of your QMS and reveal areas that need improvement. These audits should be followed by a review process to analyze the audit findings and develop improvement plans.
Keep in mind that a QMS is not a set-and-forget system. It requires ongoing attention, monitoring, and improvement to ensure it remains effective and continues to support your quality objectives.
Industries That Benefit From QMS
QMS can change the game in different sectors, but it has specific benefits for certain industries. QMS is important in manufacturing as it helps establish standardized production processes and makes the industry shine. A QMS helps manufacturers make good products consistently, reducing mistakes and waste, and improving efficiency and profits.
Similarly, the healthcare sector can also greatly benefit from introducing a QMS. A QMS can improve patient outcomes and satisfaction by standardizing procedures and reducing errors, prioritizing patient safety and care.
A QMS can provide much-needed structure and standardization for the software development industry. It ensures that each development step, from design to testing, follows quality standards. This can help reduce bugs, improve the end product, and increase customer satisfaction.
A QMS in construction ensures consistent quality in all project aspects, from materials to workmanship, making it invaluable. This can lead to safer, more reliable structures, and help build the company’s reputation for quality work.
A QMS in the food and drink industry ensures consistent quality and safety, crucial for consumer health and satisfaction. By standardizing processes, a QMS can help companies meet regulatory requirements, minimize waste, and deliver high-quality, safe products to the market.
A QMS can bring about a significant positive transformation in various industries. By establishing clear, standardized processes, a QMS can ensure quality, reduce errors, and improve efficiency, all of which are critical factors in the success of any business.
The right QMS, tailored to suit specific industry needs, can become an indispensable tool for growth and success.
LeanVlog’s Quick Video on What is QMS?
LeanVlog’s “What is QMS?” video is a great resource to check out if you prefer learning through videos.
This short video explains QMS, its importance, and the benefits an organization can gain from using it.
Ideal for beginners in the field of quality management systems, this video can serve as a stepping stone toward a more profound understanding of the subject.